方案详情
文
The quality of indexable inserts is highly dependent on their geometry and surface properties. Durability, feed rates and overall machining properties are influenced by the cutting geometry such as cutting angle and radius. Traditionally, quality assurance methods for geometry accuracy have been restricted to tactile methods. However, tactile measurement devices do not allow the measurement
of specific radii or angles due to the mechanical contact of the stylus to the surface. The optical 3D measurement device InfiniteFocus removes inaccuracies caused by tactile inspection methods. It provides highly accurate measurement of angle and profile plus the additional functionality of roughness, waviness. Also, the analysis of faults such as pits, scratches and contamination is possible. Due to the optical inspection quality, output and tool durability become approved.
G.I.T. Imaging & Microscopy 04/2005, pp. 40-41, GIT Verlag GmbH & Co. KG. Darmstadt, www.gitverlag.com, www.pro-4-pro.com Quality Assurance of Indexable InsertsThrough Surface Inspection The use of premium indexable inserts isof major importance for all manufactur-ing companies that require high metalremoval rates and high quality finishes.Therefore, as it is important that thesemanufacturing companies use inserts ofhigh quality with accurate geometry, themethods used to provide quality assur-ance is of prime importance. Optical Measurement of Angles andRadii in Contrast to Tactile Techniques The improvements in inspection resultsperformed by optical inspection are de-rived from the processes used in tactilemeasurements. Tactile measurement de-vices do not allow measurement of spe-cific radii or angles due to the mechani-cal contact of the stylus to the surface tobe analysed. Typically cutting edge radiivary between 10 um and 100 um. Thesmaller radii present difficulty for tactilesystems as the stylus has the tendency toslip from the curve leading to inaccurateresults. Also, errors can occur in angularmeasurement due to the influence of sty-lus radius friction between insert andstylus. Usually, angles and radii of thecutting edge are exactly defined beforethe insert is manufactured. Optical mea-surement allows accurate comparisonsbetween the specified dimensions andthe realities. One defines angles andradii directly on the optical colour imageand results are yielded readily at hand.As the user is able to carry out 3D mea-surements directly on the viewable opti-cal image, it is possible to improve thequality as well as measurement capabili-ties not normally associated with tactilemeasurement techniques. Fig.1: The 3D measurement device InfiniteFocus for optical measurement and inspection opens newcapabilities for quality assurance. It allows 3D measurement directly on the optical colour image. Thesubstitution of non contact optical inspection technology will remove the inaccuracies caused by tac-tile inspection methods improving quality, output and tool durability. In addition, 3D visualisation of sur-faces is provided. The 3D visualisationallows the characterisation of even largeareas. This enables a surface to beimaged, and using the built in tools fordifferential height imaging, a user is ableto observe roughness,height differences,scratches aandsurfacecontaminates.That provides an overview of the surfaceto establish if there are any defects thatrequire further examination. The viewing and measurement capa-bilities are also used in R&D, design andre-engineering. This provides benefits inensuring that the accuracy requiredfrom the cutting tools is designed into theproduct development stage and carried through to be identified in the finishedproduct. Optical Measurement and Inspection Optical 3D measurement enables a userto perform highly accurate surface mea-surements. In addition to the depth infor-mation, a dense and robust 3D surfacereconstruction is feasible. Unlike tactilemeasurement tools, the optical measure-ment technique provides meaningful, ro-bust and highly accurate data from allsurfaces whether they are flat, curved orangled. Varying sizes of objects can beviewed due to variable magnification.The X,Y,Z stage provides a movement Fig.2: The 3D measurement device allows the optical measurement ofangles and radii of cutting edges directly on the optical colour image.Additionally, it provides analysis capabilities such as profile,area,volumetric and roughness measurements. In contrast to tactile measurement techniques, results yield by optical inspection are highly accurate and reliable. range of 120 mm x 53 mm at a maximumscan height of 70 mm. Results up to 20nm in z are feasible. The colour focussensor technology achieves 3D analysismeasuring routines to be performed di-rectly on the optical image allowingcolour verification of height. The opticalinspection technique offers comprehen-sive measurement capabilities such asprofile, area and volumetric analysis.Roughness measurement can also be ob-tained according to EN ISO 4287/4288. As far as its handling is concerned, In-finiteFocus is very user friendly. The useris able to extract, a profile on the optical2D image and determine angles, radiiand other values, e.g. lines, circles orpolygons via a mouse click. Traceability is provided with a PTBapproved calibration tool, making it suit-able for applications where such trace-ability is essential. Summary Cutting inserts for metal cutting made oftungsten carbide allow high-perfor-mance cutting. The outstanding hard-ness and wear resistance of the materialassures high cutting speed, extendedtool-life, and short machining time. Asfar as quality assurance of high-perfor-mance cutting inserts is concerned, opti-cal measurement of surfaces can providemeaningful surface analysis since it re-moves inaccuracies caused by tactile in-spection methods. With its optical mea-surement device.2,Alicona Imagingenables the highly accurate measure- Fig.3: The 3D measurement device also providesrobust and dense 3D visualisation capabilities ofany solid and reflective surface. Examining thesurface of a cutting edge in 3D makes it veryeasy to spot surface properties such as rough-ness, height steps, scratches or other contamina-tions. ment of cuttingedges angles and radii.The user carries out 3D measurement di-rectly on the optical colour image whichsignificantly improves measurement re-sults in contrast to tactile techniques.Measurements up to 20 nm z-resolutionare achievable despite steep flanks andgreatly varying surface reflection prop-erties. Indexable inserts that are qualityassured with optical inspection can beused with confidence in turning, millingand drilling operations, ensuring highquality and reproducible machining re-sults. Mag. Astrid KrennSales & MarketingAlicona Imaging GmbHTeslastraBe 88074 Grambach/Graz, AustriaTel.+43 316 4000 700·Fax +43 316 4000 711sales@alicona.com·www.alicona.com
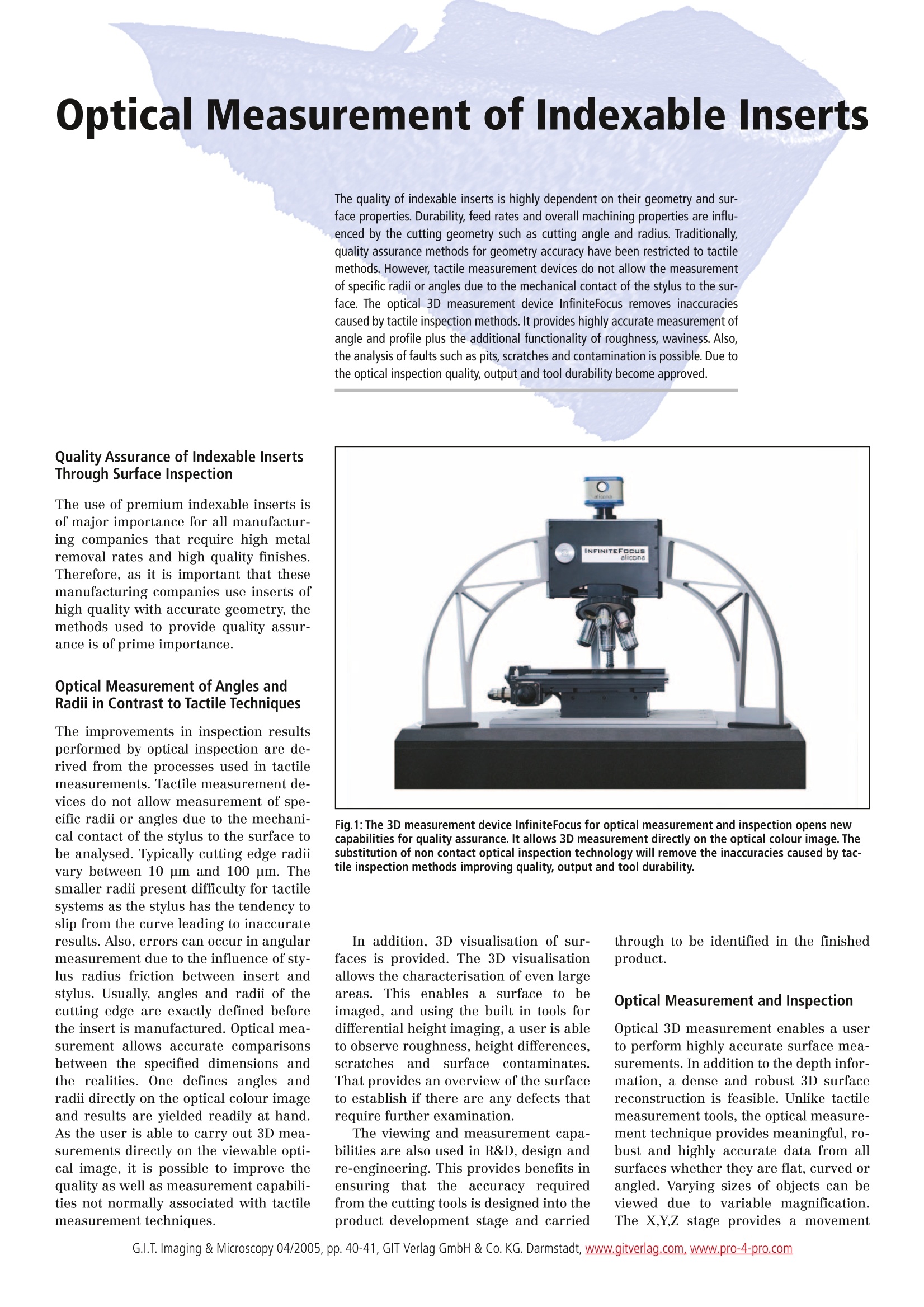
还剩1页未读,是否继续阅读?
北京东方德菲仪器有限公司为您提供《可转位刀具中切削角和半径检测方案(轮廓仪)》,该方案主要用于生活用品中切削角和半径检测,参考标准--,《可转位刀具中切削角和半径检测方案(轮廓仪)》用到的仪器有